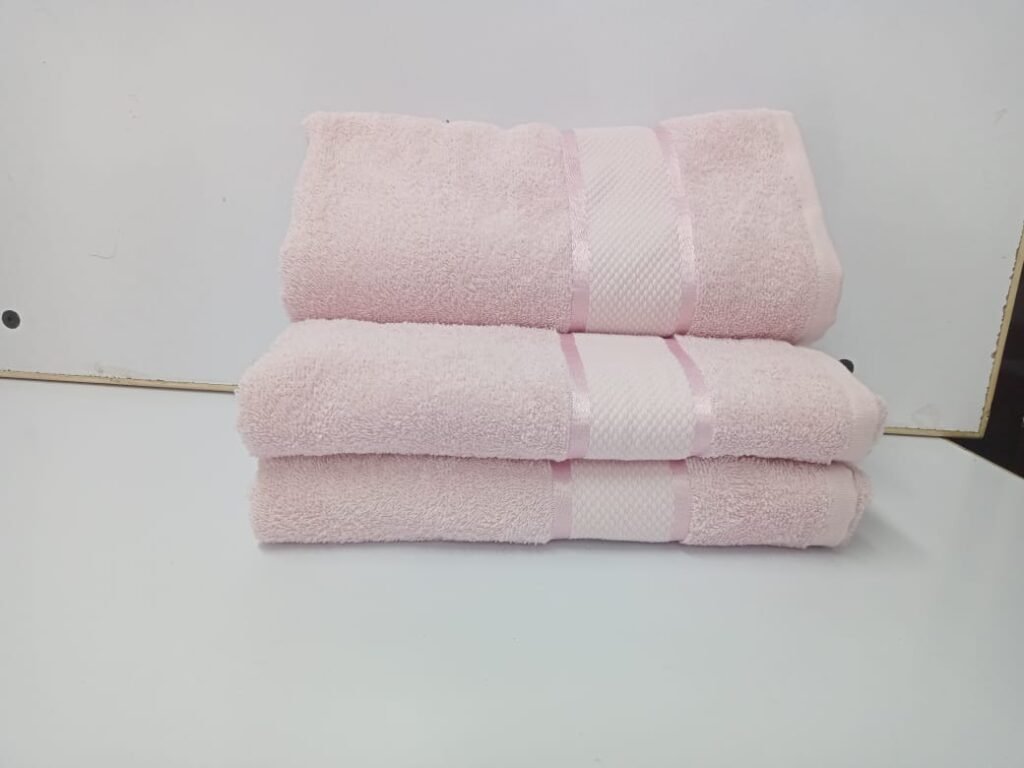
Towel manufacturing is the process of creating soft, absorbent, and durable towels, an essential part of our daily lives. It involves selecting quality raw materials, weaving, dyeing, finishing, and rigorous quality control to produce towels that meet various standards and consumer expectations. The manufacturing process includes steps like yarn selection, weaving techniques, sizing, dyeing, cutting, hemming, and extensive quality testing to ensure the towels are comfortable, resilient, and meet required quality standards. Towel manufacturing combines artistry and science to create the perfect balance of aesthetics and functionality in our everyday towels.
Table of Contents
1-Design Selection Process for Towel Manufacturing:
Weave-able designs for towels can be categorized into two primary types: dobby and jacquard patterns. Each requires different software tools and techniques for their creation.
Dobby Designs:
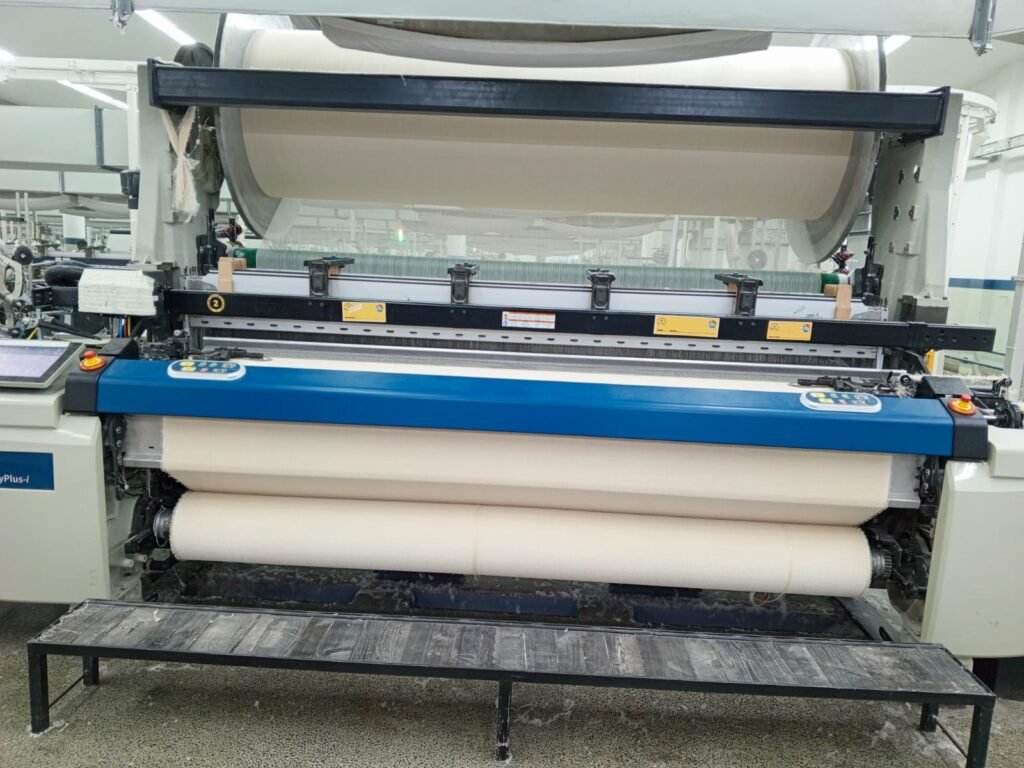
Dobby designs are relatively simpler compared to jacquard patterns and are often used for more basic, repeating patterns on towels. Creating dobby designs involves the following steps:
Design Concept: Begin with a concept for your pattern. Dobby designs typically consist of simple, repeating motifs, borders, or geometric shapes.
Digital Design Software:
To create dobby designs, you can use graphic design software like Adobe Illustrator, CorelDRAW, or specialized weaving software such as Pointcarre, NedGraphics, or Textronics Design System. These programs allow you to draw and manipulate the design on a grid, specifying colors and weaves.
Color Selection:
Choose the colors you want for your design and indicate them within the software. The software will help you create a color palette that can be translated into the weaving process.
Tie-Up and Lift Plan:
Define the tie-up and lift plan, which determines how the warp threads will be lifted to create the desired pattern. This information is typically created within the weaving software.
Simulation and Analysis:
Most weaving software offers simulation tools that allow you to preview how the design will appear on the fabric. You can make adjustments as needed to achieve the desired result.
Export Files:
Once the design is finalized, export the design files in the appropriate format for the weaving loom. Common formats include. JPG, .TIFF, or Dobby files.
Jacquard Designs:
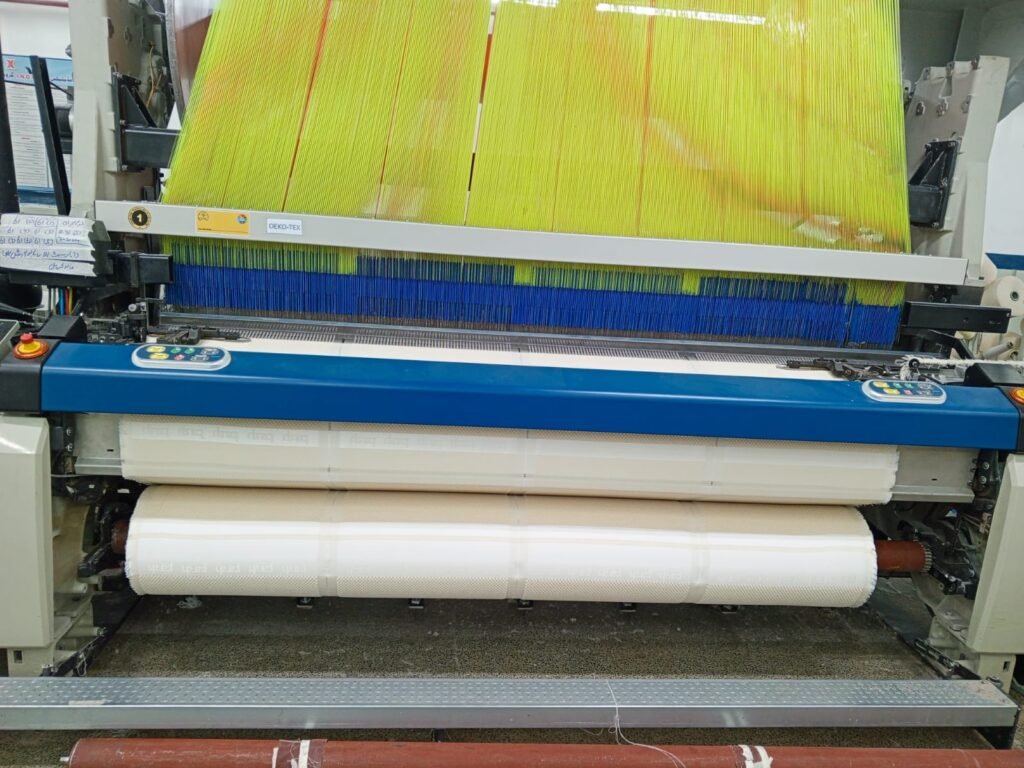
Jacquard designs are more complex and intricate, often involving detailed imagery and fine details. These designs are commonly used in high-end and luxury towels. Creating jacquard designs involves the following steps:
Concept and Design:
Start with a clear concept for the jacquard design, as these patterns can be highly detailed and realistic. Design motifs, images, or intricate patterns.
Specialized Jacquard Software:
Start with a clear concept for the jacquard design, as these patterns can be highly detailed and realistic. Design motifs, images, or intricate patterns.
Image Processing:
For detailed imagery, you may need to prepare and process the images or motifs in graphics software like Adobe Photoshop or CorelDRAW.
Color and Weave Assignment:
Assign colors to each pixel or element in the design and specify the weave pattern. Jacquard software offers intricate control over color and weave combinations.
Machine Interface:
Jacquard looms are controlled by dedicated computer interfaces that communicate directly with the design software. Ensure that your design files are compatible with the loom’s interface.
Simulation and Analysis:
Jacquard design software often includes simulation features that allow you to see how the design will appear on the fabric and make any necessary adjustments.
Export Files:
Export the finalized design files in the format compatible with the specific jacquard loom’s software and hardware.
2-Yarn Selection for Towel Manufacturing:
Selecting the right yarn count is a crucial aspect of terry towel production, influencing the towel’s quality, texture, and absorbency. Different components of the towel, such as pile, weft, border, and warp yarns, often require specific yarn counts to achieve the desired characteristics.
Here are some hints for selecting appropriate yarn counts for each type of yarn in terry towel manufacturing:
Pile Yarn Counts selection for towel manufacturing:
Pile yarns make up the raised loops on the surface of the towel, responsible for its softness and absorbency. In general, thicker pile yarns are used for plush and absorbent towels. Typical pile yarn counts for terry towels range from 10s to 18s Ne (New English Cotton Count), with a higher count indicating finer and softer pile yarn. We often used double pile yarn counts like 18/2, 20/2, and 24/2 for institutional towels like hotels and hospitals.
Weft Yarn Counts selection for towel manufacturing:
Weft yarns run horizontally across the towel and contribute to its smooth texture. Weft yarns are usually finer than pile yarns, providing a contrasting texture. Common weft yarn counts for terry towels range from 10s to 16s Ne.
Border Yarn Counts selection for towel manufacturing:
Border yarns are used for decorative borders or hems and require added strength and durability. Coarser yarn counts are often chosen for border yarns, typically ranging from 6s to 12s Ne or higher.
Warp Yarn Counts selection for towel manufacturing:
Warp yarns create the towel’s foundational structure, and their selection influences the towel’s thickness and weight. Warp yarn counts commonly fall in the range of 20s to 40s Ne, depending on the desired characteristics of the towel.
3-Warping process for towel manufacturing:
Warping is the initial stage in crafting terry towels. To get the long warp threads ready, we use a sectional warping machine. When it comes to creel machines, we have two common types: H-type and V-type. The choice between these two depends on the manufacturing setup. H-type creels are often preferred for their practicality and efficient use of space.
In the warping process, our goal is to evenly space and wind the yarn onto the beams. Once that’s done, we’re all set for the next step, which is sizing the yarn & and making it ready for the weaving process.
4-Sizing Process for towel manufacturing:
The sizing process is a crucial step in preparing yarn for weaving. We use a machine called a sizing machine to add a protective coating to the yarn. This coating, typically made of starch, ensures the yarn stays strong and doesn’t break during weaving. Sizing is necessary because it improves the yarn’s strength, making it more resilient and preventing breakage, which is important for creating high-quality towels.
5-Drawing-In Process for towel manufacturing:
Drawing in for towels involves threading the warp yarns through the loom’s heddles and reed. It’s like weaving the yarn’s path through a series of eyes and a comb-like structure. This sets up the warp yarns for weaving.
Loom Article:
The loom article refers to the fabric being woven on the loom, which, in the context of towel manufacturing, is the towel itself. It’s the result of the weaving process that turns yarn into fabric.
Knotting:
Knotting is a method used to securely join the ends of yarn when transitioning between rolls or spools. It ensures a continuous supply of yarn to the loom without interruptions in the weaving process.
6-Weaving process for towel manufacturing:
The weaving process for towels involves interlacing warp and weft yarns on a loom to create the fabric.
Pile Weave for towel manufacturing:
When it comes to terry towels, a specific type of weave, known as terry weave, is used for the plush, absorbent pile. Variations like 3-pick terry, 4-pick terry, and others refer to how many weft yarns are used to form each loop in the pile. More picks result in a denser and softer pile, enhancing the towel’s absorbency. But the most common type is 3-pick terry.
End Hem Weave for towel manufacturing:
A straightforward choice is a plain weave to reinforce the end hems or edges of the towel. It’s simple and strong, ensuring the edges don’t fray. However, for a touch of elegance, decorative patterns like satin or twill weaves can be used.
Border Weave for towel manufacturing :
Towel borders offer room for creativity. They can incorporate various weave patterns, including plain, twill, or satin borders. The choice depends on the desired design and aesthetics of the towel’s borders.
Folding section:
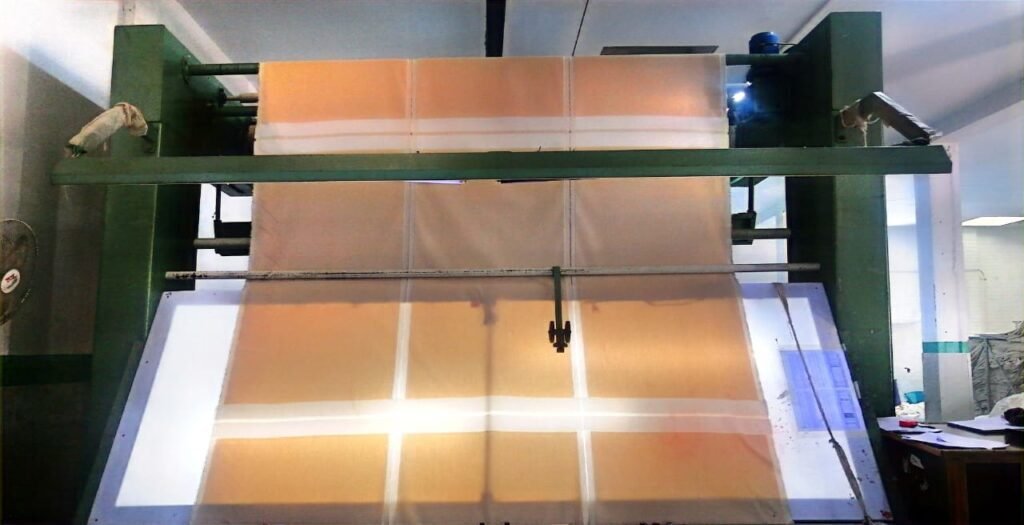
The folding process in weaving is a critical post-weaving step where the woven fabric is carefully and systematically checked. In this case, each roll of fabric produced by every loom is thoroughly checked for defects. Any defects or irregularities in the fabric is identified and addressed. Additionally, each roll is weighed to ensure it meets specified weight standards and then folded systematically.
This is typically done to prepare the fabric for the next stage in production, which could be packaging in greige form or further processing or dyeing.In some textile manufacturing settings, especially in the folding section, additional quality control measures are implemented during the folding process. Once the inspection, defect identification, and weighing processes are completed, the rolls of fabric are sent to the next stage in the dyeing section. These quality control measures help ensure that only high-quality fabric moves forward in the production process, and any deviations from the quality standards can be addressed before further processing
7-Lot-Making Process for Dyeing in Towel Manufacturing:
The lot-making process for towels focusing on dyeing machine capacity, same size, same order, and same GSM involves efficiently producing batches of towels with identical specifications. After receiving a customer’s order, towels of the same size and GSM are sourced, and a specific dye color is chosen to meet the order requirements. These towels are then dyed in the same color, maximizing the dyeing machine’s capacity and ensuring uniformity. Following quality control checks, if there is a set packing requirement, all sizes are bundled together with the help of a sewing machine and dyed in the same color for the same customer, streamlining production and meeting precise customer demands for color.
8-The dyeing process of towel Manufacturing :
The dyeing process for towels involves several essential steps, specific machines, various dye types, and necessary chemicals. Initially, the towels are prepared by washing and scouring to remove impurities and finishes. Dye selection is critical, with different dye types used for various fabrics such as cotton or cotton blends. Common dye types include reactive dyes, vat dyes, or direct dyes, depending on the fabric’s composition and the desired color. The dye bath is prepared by dissolving the chosen dye in water, with the addition of necessary chemicals and auxiliaries to aid the dyeing process.
The towels are then immersed in the dye bath and agitated to ensure even dye distribution. This dyeing process can take place in specific dyeing machines, such as an Exhaust dyeing machine (thies machines & MCS machines) for high-speed dyeing or a beck dyeing machine for batch dyeing. Following dyeing, the towels undergo rinsing to remove excess dye and multiple wash cycles to fix the color and enhance colorfastness.The dye type and machinery choice depends on the specific fabric and color requirements. Overall, the dyeing process ensures that towels are uniformly and vibrantly colored while meeting quality standards, making them suitable for various applications.
9-The Finishing process of towel manufacturing :
The finishing process for towels involves several steps, specific machines, like Pentack, Englada, Biacklani, and various chemicals to enhance the texture and appearance of the dyed fabric. After the dyeing process, towels may undergo additional treatments such as softening, drying, or calendaring. Softening is often achieved through a softening machine, which uses steam and chemicals to improve the fabric’s feel. Drying machines, such as tumble dryers or conveyor dryers, are employed to remove excess moisture from the towels. Calendering machines, which apply heat and pressure, can further smooth and improve the fabric’s surface but may be used in rare cases. The finishing process ensures that towels not only meet color specifications but also achieve the desired softness and texture for optimal comfort and usability.
10-The Slitting process of towel Manufacturing:
The towel slitting process is a crucial step in the textile industry, involving the precision cutting of large rolls of fabric into narrower strips, ensuring the creation of uniformly sized towels. Various cutting-edge slitting machines play a pivotal role in this process, each with unique features designed to enhance efficiency and accuracy.
One notable slitting machine is the Texpa Towel Slitting Machine, known for its reliability and precision. It’s equipped with advanced cutting mechanisms that ensure clean and straight cuts, contributing to the overall quality of the towels. The Azeemo Towel Slitter is another prominent player in this field, offering versatility and high-speed cutting capabilities, making it suitable for large-scale production.
The Kandai Towel Slitting Machine is recognized for its innovative design and user-friendly interface. It allows for customization of the cutting width, accommodating diverse towel dimensions with ease. Meanwhile, the Schmale Towel Slitter stands out for its efficiency in handling a wide range of fabrics, providing consistent results in terms of size and quality.
Tept and Bando are also noteworthy names in the towel-slitting machinery landscape. The Tept Towel Slitter is revered for its precision engineering and adaptability to various fabric types, ensuring a smooth and accurate slitting process. The Bando Towel Slitting Machine is known for its durability and robust performance, meeting the demands of high-volume production.
11-The Length hemming process for towel Manufacturing:
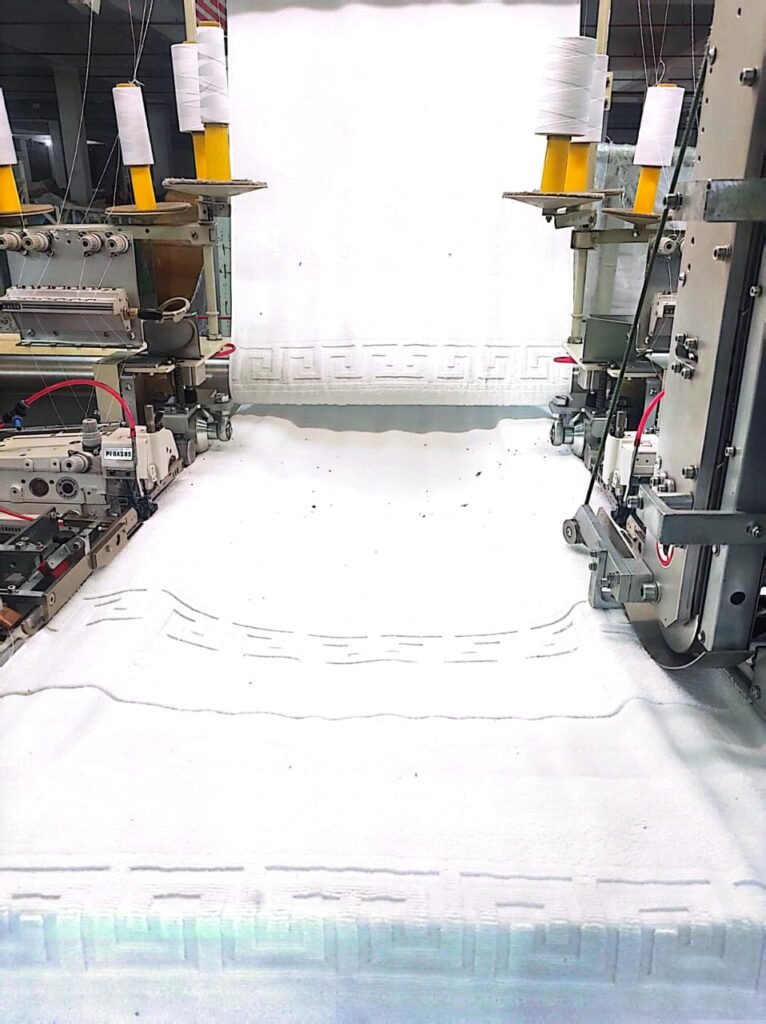
The towel-length hemming process is a critical stage in the production of high-quality towels, ensuring that the edges are neatly finished for a polished and durable final product. This process involves the use of advanced hemming machines, with several reputable names leading the industry.
In conclusion, the towel-length hemming process is elevated by cutting-edge machines such as Texpa, Azeemo, Kandai, Schmale, Texpt, and Bando. These machines play a pivotal role in achieving precision and efficiency, resulting in towels with neatly hemmed edges that meet the exacting standards of the textile industry. Their advanced features make them indispensable in the production of towels, contributing to the overall quality and appeal of the final product.
12-The cross-hemming process for towel Manufacturing:
Cross-hemming or stitching in towel production refers to the process of securing and finishing the fabric edges in a decorative cross-stitch pattern. This technique is efficiently carried out using a single-needle lockstitch machine. The machine’s precise needlework creates a visually appealing cross-hem, enhancing the towel’s overall aesthetics while ensuring a durable and reinforced edge. This method not only adds a decorative touch but also contributes to the towel’s structural integrity, combining functionality with a pleasing design.
13-The Towel grading process for Towel Manufacturing:
Towel grading involves a meticulous assessment of each towel’s quality based on established criteria. This process identifies and categorizes towels according to size, color consistency, fabric integrity, and overall workmanship. Grading ensures that only towels meeting the desired specifications progress to subsequent stages, maintaining a high standard of quality throughout the production line
14-The Towel Folding Process for Towel Manufacturing:
Towel Folding is a precise and standardized procedure where towels are carefully folded into uniform shapes. This not only optimizes storage and transportation but also contributes to the towels’ visual appeal when presented to consumers. The folding process requires attention to detail to achieve consistent dimensions and neatness, reflecting professionalism and quality in the final product.
15-The towel Packing Process for Towel Manufacturing:
The packing stage involves bundling and preparing towels for distribution. It includes the careful arrangement of folded towels into packaging that aligns with customer requirements. Efficient packing not only safeguards the towels during transit but also facilitates ease of handling and inventory management. The use of branded packaging materials further enhances the towels’ market presentation, reinforcing the overall value of the product.