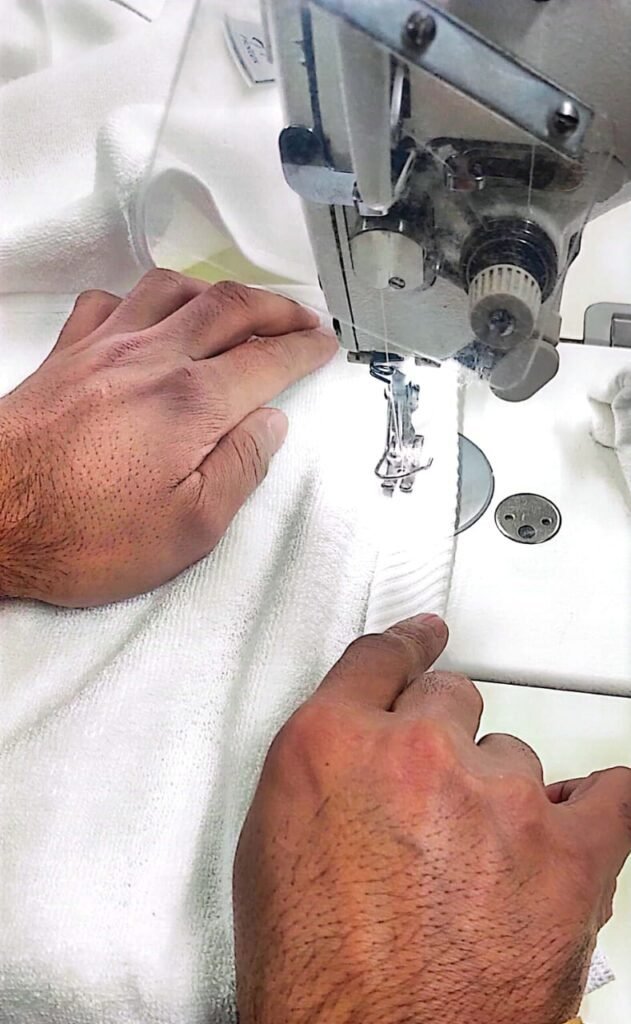
Stitching on towels:
Stitching on towels are meticulously manufactured towels where the edges on both sides, lengthwise and crosswise, are secured through stitching and hemming. The side stitching is referred to as long hemming, while cross stitching is known as end hemming or cross hemming. The primary purpose of this stitching is to reinforce the towel, providing strength and durability. This stitching not only enhances the towel’s robustness but also imparts a distinctive appearance, elevating its overall appeal and improving its adaptability.
Length hem, stitching on towels with class 300:
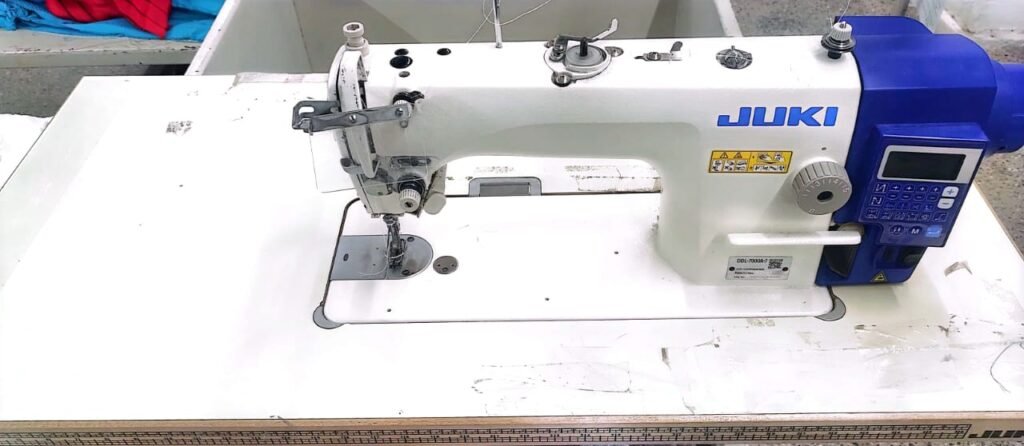
The length hem, stitching on towels is commonly done using the Class 300 stitching method, a widely used technique employed by lock stitching machines such as the renowned Juki and Brother Machines. In this process, a needle thread passes through the material and locks with the bobbin threads, forming secure lock stitching on the towels. This stitching can be either single-needle lock stitching or double-needle lock stitching, with the latter being more secure. To ensure precision in hemming, a folder attachment can be utilized, although skilled tailors with experience and expertise can also create hems by hand. It is advisable to use folders for accuracy, but the choice ultimately depends on the tailor’s proficiency.
Advantages of class 300, stitching on towels:
Utilizing the Class 300 stitching method for towels ensures a high level of security, as each stitch per inch (SPI) is firmly locked with the bobbin threads. In the rare occurrence of a skip stitch or jump stitch, only one stitch becomes loose, having minimal impact on the overall stitching and hemming process. This characteristic makes the stitching exceptionally durable, contributing to an extended lifespan for the towel.
Disadvantages of class 300, stitching on towels:
One drawback of the Class 300 stitching method lies in the machine specifications, where the RPM (revolutions per minute) ranges from 3000 to 4500, and the stitch length is limited to 2.1 mm to 3.6 mm. This makes it unsuitable for continuous-length hemming, leading to production loss. Additionally, frequent bobbin changes are required, contributing to increased downtime and ultimately affecting overall production efficiency.
Furthermore, if the machine lacks a built-in folder attachment, resulting in an uneven hem, precision may be compromised. Therefore, it is crucial to consider these factors when using Class 300 machines for stitching, ensuring both efficiency and accuracy in the production process.
Length hem, stitching on towels with class 400:
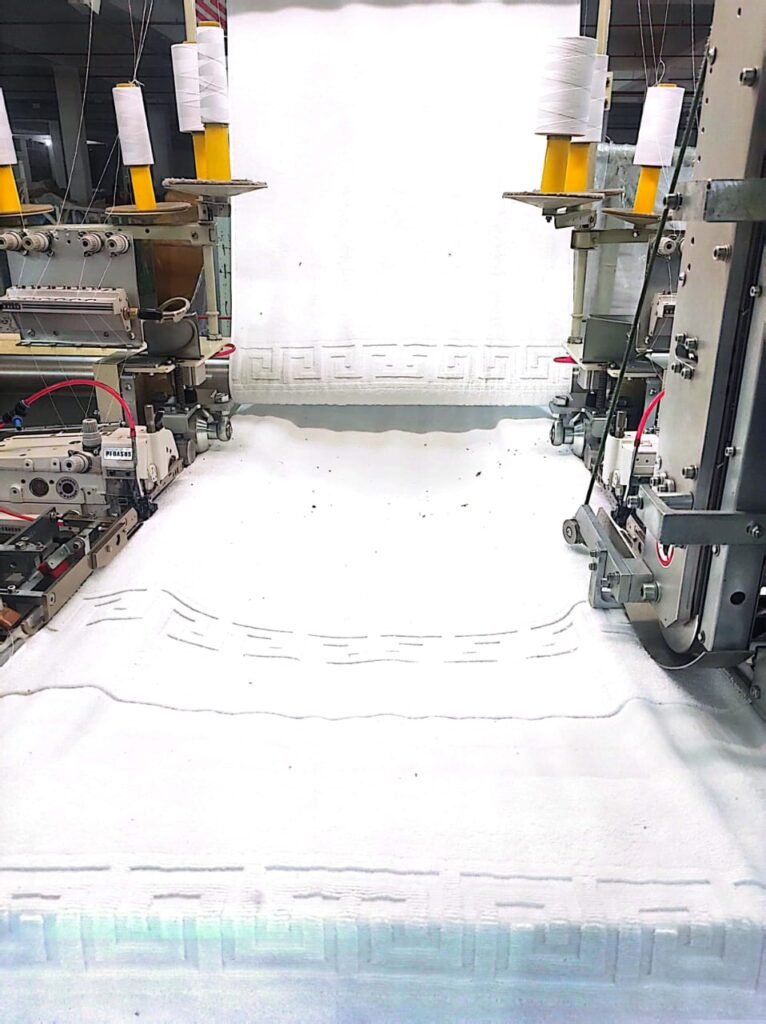
The stitching on towels with Class 400 is recognized for its enhanced productivity and accuracy, making it a widely adopted choice in the towel manufacturing market. This type of stitching, known as multi-thread chain stitch, involves the needle thread passing through the material, interloping, and interlacing with loops created by other sets of thread from the loopers.
To create hems on towels, folders are employed on both sides. Class 400 machines, such as Texpa, Bando , Tept, and Azeemo, typically feature two heads—left and right. This setup allows both sides of the towels to be stitched simultaneously; the right side is stitched with the right head, and the left side is stitched with the left head.
Class 400 machines offer the flexibility of providing single stitching on both sides or double needle stitches on both sides. Some manufacturing companies in this class also offer additional features like label and hanger attachment facilities on the side hemming. The inclusion of sensors ensures precise guidance for the machines, ensuring accurate placement and application of labels and hangers as needed on the side hemming. This combination of efficiency and accuracy makes Class 400 a preferred choice in the towel manufacturing industry.
Advantages of class 400, stitching on towels:
Class 400 machines offer superior performance with high output and flexibility. They allow for remote maintenance, ensuring convenient and efficient upkeep. These machines are equipped with chain stitch technology, delivering a smooth finish on thick borders, thanks to the installed cutter or trimming devices at both heads.
The precision of hems is notably high, thanks to the incorporation of folders and sensors in Class 400 machines. Additionally, these machines prioritize cleanliness by utilizing pneumatic-pressure devices to eliminate unwanted loose threads. Waste storage boxes contribute to a tidy working environment. In summary, Class 400 machines combine efficiency, precision, and cleanliness, making them a top choice for various applications.
Disadvantages of class 400, stitching on towels:
These machines in the Class 400 category are designed for continuous stitching, making them highly efficient. However, they come with certain challenges.
Firstly, the occurrence of skip and jump stitches poses a significant issue. If a skip stitch occurs, there is a risk of the entire stitching unraveling after washing, rendering the towel unusable.
Secondly, these machines operate using pneumatic air pressure. A consistent and uninterrupted supply of air is crucial for their operation. Any fluctuations or interruptions in the air supply can lead to a shutdown of the entire process.
Thirdly, being electronically controlled machines, they require regular maintenance. Daily, weekly, and monthly preventive maintenance is essential. If not conducted on time, it can result in a series of problems, eventually leading to a shutdown and causing production losses. Proper and timely maintenance is key to ensuring the smooth and uninterrupted functioning of these machines.
Cross hem, stitching on towels with class 300:
Cross hem, also known as end hemstitching on towels, is commonly and frequently carried out using Class 300 machines. This can involve either a single-needle lock stitch or a double-needle lock stitch. Typically, this process is performed without the use of folders and attachments. The towels are first cut into individual pieces, and then each piece is hemmed, incorporating the stitching on the hem. Additionally, brand labels, paper labels, and logo labels are applied during this stage. The versatility of Class 300 is evident in its use for various types of hems, different measurements, and single-piece hemming, making it well-suited for cross-hemming or end hemming.
Moreover, the short width and more frequent pauses required for applying labels and hangers make Class 300 machines a practical choice. Among the popular Class 300 machines, Juki and Brother stand out as widely utilized brands in the towel stitching market. Their reliability and efficiency make them preferred options for achieving quality cross-hemming or end hemming on towels.
Frequently asked questions" stitching on towels":
What stitching methods are commonly used for towels?
There are several stitching methods employed for towels, with popular options including chain stitch and lock stitch. The choice often depends on the specific requirements of the towel and the machinery used in the manufacturing process.
How does stitching contribute to the durability of towels?
Stitching plays a crucial role in reinforcing the edges and hems of towels, enhancing their overall strength and durability. Proper stitching ensures that the towel can withstand regular use and washing, and maintains its quality over time.
What is the significance of using Class 300 or Class 400 machines for towel stitching?
Class 300 and Class 400 machines are known for their efficiency and precision in towel stitching. Understanding the advantages of each class helps manufacturers choose the right machinery based on their production needs, such as volume, flexibility, and the desired stitching pattern.
How do labels and logos get applied during the stitching process?
Labels and logos are often applied during the stitching process using specialized machinery. Manufacturers may utilize features like label attachment facilities on certain machines, ensuring accurate placement and application of labels and logos during the stitching of towels.
What challenges are associated with continuous stitching on towels?
Continuous stitching on towels can pose challenges such as the risk of skip or jump stitches, potential unraveling after washing, and the need for consistent pneumatic air pressure. Understanding and addressing these challenges are crucial for maintaining the quality and efficiency of the stitching process.