The Definition Of Sizing:
Sizing is the process of applying an adhesive material to paper or textiles to enhance binding properties and strength. In the textile industry, sizing is applied to warp yarns to increase their strength, allowing them to withstand the high tension and pressure experienced during the weaving process. This sizing can be easily removed using desizing agents during the bleaching and dyeing stages in processing units.
The Purpose of Textile sizing:
- To achieve the required number of ends on the weaver beam.
- Application of a coating to the yarns.
- Enhance the tensile strength of the yarns.
- Reduce yarn hairiness.
- Increase the weight of the yarns.
The Required Properties For size material:
- Should be easily removable.
- Must have adhesive properties.
- Should be non-toxic.
- Should provide antistatic properties.
- Needs to offer flexibility.
- Should exhibit good drying ability after application.
- Should not alter the color or shade of the fabric.
- Should be cost-effective and readily available.
- Must not degrade or damage the yarn.
The Ingredients Needed For Sizing Recipe:
- Starch (050500): Low viscosity, high penetration, suitable for fine yarn counts.
- Starch (030700): High viscosity, used for coating, suitable for coarser yarn counts.
- PVA Elvanol.
- Galtex.
- ACR-140 (Acrylic).
- Textile Wax AW-190.
The Mchines Used For The Sizing process :
There is an extensive list of machines available for the sizing process; however, two of the most renowned machines for this purpose are Benninger and Karl Mayer. We will provide a detailed comparison of the functions of these machines to facilitate a better understanding of their components and operations.
The Cylinders on The Sizing machine
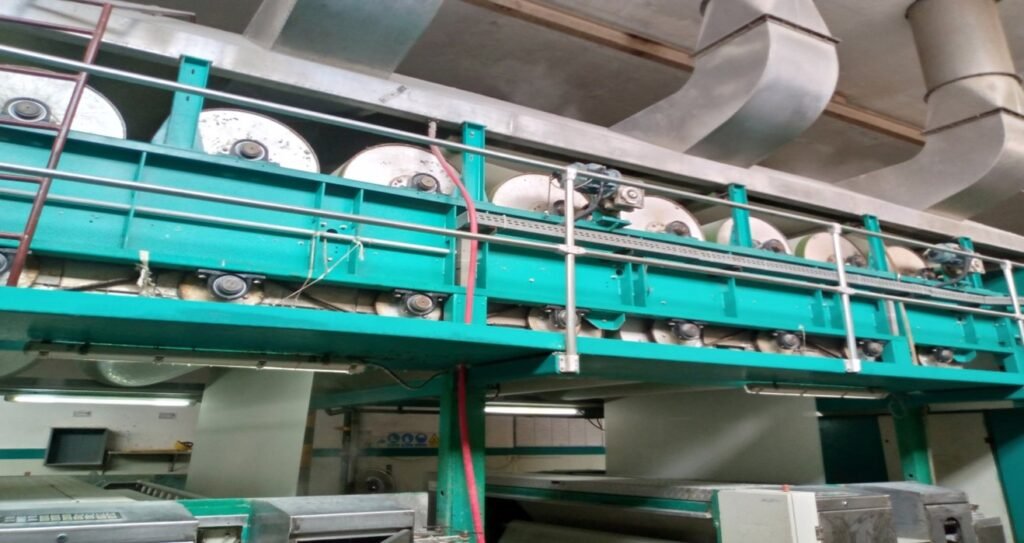
The Cylinders comparison of Benninger and karl Mayer Sizing machine:
Sr. No | Cylinder Type | Benninger | Karl Mayer | Karl Mayer (pro size) |
---|---|---|---|---|
1 | Mini drying cylinders | 4 | 4 | Nil |
2 | Drying cylinders | 14 | 14 | 20 |
3 | Pre-wet return | 2 | 2 | Nil |
4 | Pre-wet exit | 2 | 2 | Nil |
5 | Immersion | 2 | 2 | Showering |
6 | Lateral lower and upper squeezing | 4 | 4 | 4 |
7 | Lateral squeezing pre-wet | 4 | 4 | Nil |
The Motors Details & Functions :

The Motors Details & Functions of Benninger and Karl Mayor Sizing Machine:
Section of sizing m/c | Benninger
| Karl Mayor | |
---|---|---|---|
Creel | 2 motors for mono rail, (one for lifting/lowering one for forward and backward movement) | 2 motors for mono rail, (one for lifting/lowering one for forward and backward movement) | |
Double Pre-wetting box | Two motors for feeding rollers. Two motors for pressing rollers. Two motors for squeezing rollers of Pre-Wetting Box. Two motors for water circulation | Two motors for feeding rollers. Two motors for lower squeezing rollers of Pre-Wetting Box. Two motors for water circulation. | |
Double Size Box | 4-One motor for reversing the size liquor back into the tank at the end of a set for both size boxes (for the pump) | 1-Two motors for the final squeezing rollers 2-Two motors for the circulation pumps of the size liquor 3-One motor for returning the size liquor to the tank after the completion of a set for both size boxes (for the pump) | |
Drying Section | One motor dedicated to the final six drying cylinders Three motors allocated for ventilation (exhaust fans) | One motor dedicated to the final six drying cylinders Three motors allocated for ventilation (exhaust fans) | |
Waxing Assembly | One motor for waxing roller. | One motor for waxing roller. | |
Head Stock |
| 1-Two motors for beam drive 2-Two motors for beam lifting 3-Two motors for block movement or adjustment 4-One motor for beam safety 5-One motor for the taping device 6-One motor for the drag roller 7-Three motors for comb movement (one motor for comb opening and closing, one motor for vertical movement, and one motor for horizontal traversing) | |
Cooking Section | One motor for stirring the cooker One motor for stirring the storage tank One motor for transferring the sizing recipe from the cooker to the storage tank |
| |
Warp tension zone And Factors:
The warp sheet is subjected to significant tension during the sizing process, which affects the elongation and stretch of the yarn. The applied tension should be comparable to the tensile strength of the yarn to minimize excessive breakages during sizing. A sizing machine has six identified tension zones.
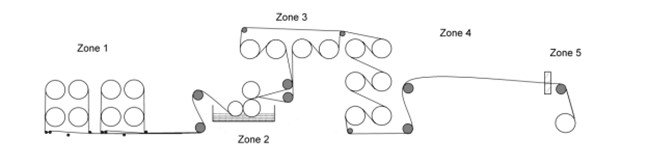
SR# | Name Of Zone | Range | Factors
|
---|---|---|---|
Let Off Zone | From 1st warping beam of creel to drag roll at size box | 5 – 7 | |
In-Let Zone | From drag roll to the first nip | 3 – 4 | |
Wet Zone | From 2nd nip to the first drying cylinder | 3.5 | |
Dry Zone | From the last drying cylinder to the guide roll (headstock) | 11 – 14 | |
Winding Zone
| From guide roll to weaver’s beam | 18 –24 | |
Pressing Zone
| Tension by press trolley on the beam
| 16– 20 |
Warp tension zone And Calculations:
Tension can be calculated at any zone by the following formula
Tension = W Warp x Factor,
Where
W Warp = (𝑇𝑜𝑡𝑎𝑙 𝑒𝑛𝑑𝑠 × 1.0936 / 840 × 𝑌𝑎𝑟𝑛 𝑐𝑜𝑢𝑛𝑡) × 453.6
W Warp = 15000 × 1.0936 / 840 × 40) × 453.6
W Warp = 221.5 g/m.
Q: From where we get 453.6 values in this formula?
One pound is equal to 453.592 grams. This is 453.6 approximately for pounds to gram conversion we use it.
Now, the pressure of diverse zones is calculated as:
Let-off tension = 6 × 221.5 = 13.29
In-let tension = 3 × 221.5 = 664.5
Solid Concentration% Formula:
Weight of solid Contents/ Weight of Total solution x 100
Size Material | Solid Content % | Quantity Ratio |
ACR. | 50% | 3 kg |
Starch | 85% | 60 kg |
Wax | 100% | 2 kg |
Amount of Water = 875 Kg
Total recipe = 940 Kg
1 batch cooking will be done.
Conc. % = 65 Kg/940=6.9%.
Weight of Un-sized yarn Formula:
Weight of un-sized yarn = Length × Total.Ends / 768.1× yarn COUNT
Weight of sized yarn Formula:
Weight of size substances = Sized yarn weight – Un-sized warp weight
Procedure Of Sizing Process:
- Obtain warped beams from the warping section.
- Prepare the maximum number of warped beams based on the sizing creel capacity and production demand.
- Attach the yarn from each beam to the sizing machine.
- Inspect the sizing chemical thoroughly.
- Apply the sizing chemical to the warp sheet.
- Verify the functionality of the drying section to ensure proper drying of the warp sheet.
- Set the tension according to the designated zones.
- Wind the warp sheet onto the beam.
- Transfer the beam to the storage area for the subsequent weaving process.
Conclusion:
We utilize warped beams, which are straightened to remove any distortions, and secure them to the creel of the sizing machine. Subsequently, the sizing process is initiated. Due to the machine’s capacity limitations, we employ a maximum of 28 beams simultaneously for the above sizing machines.