Table of Contents
the definition of warping:
Warping is the process of organizing a specific number of warp yarns of similar length so they can be gathered onto a single warp beam. This beam is then used in the sizing or weaving process to create fabric or towels.
the Objectives of warping:
- Prepare a warp by selecting and organizing a set number of warp threads to the specified length.
- Arrange these threads in the required sequence.
the Basic Requirment of warping:
warping Machine:
Creel Machine:
Head stock:
warper beams:
Yarn Bags:
warping Machines:
Types of warping Machine:
1-Sectional or Pattern Warping (conical drum or dresser warping).
2-High speed/ Beam/ Direct Warping (preparatory beam warping).
Machine Drives of Warping Machine:
- One main motor is used to drive the warped beam.
- Three motors operate the comb functions: one for opening, one for traversing, and one for moving up and down.
- Two motors are responsible for loading and unloading beams.
- One motor powers the hydraulic pump for the braking system.
- Two motors control the creel change system.
- Two motors are used for the pre-tensioning system.
Creel Details for wraping :
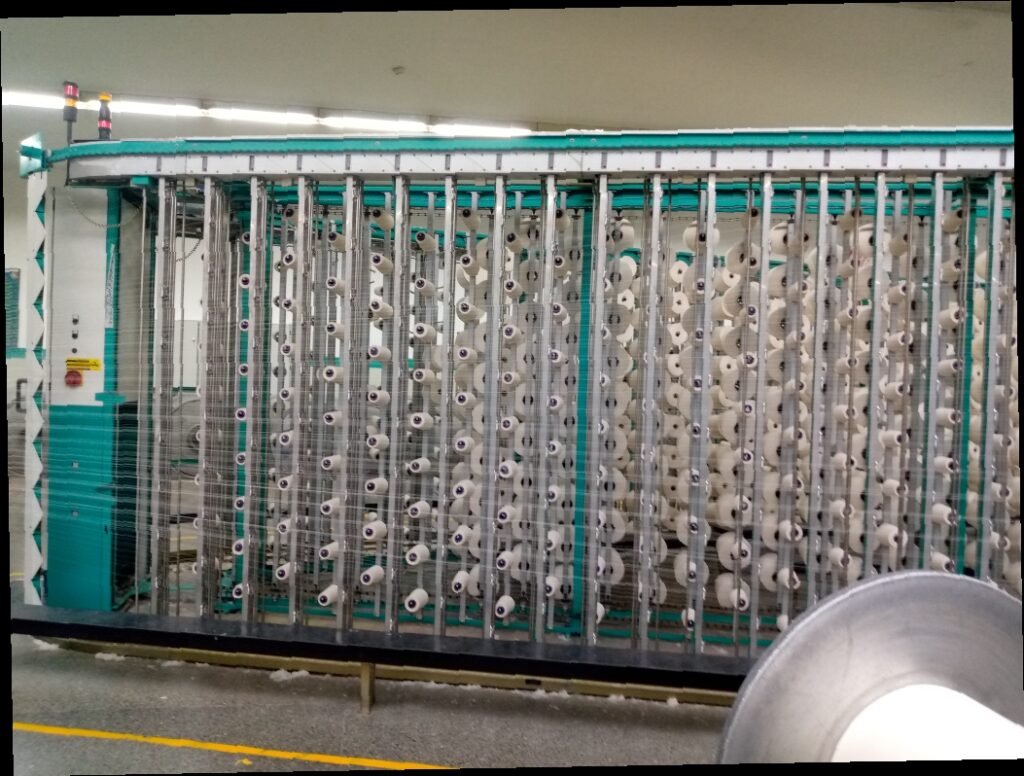
SR# | Specs | Machine-1 | Machine-2 | Machine-3 |
---|---|---|---|---|
1 | Brand name | 4 STAR JIANGYIN | ||
2 | Model | 2020 | 2021 | 2016 |
3 | Country | china | china | Switzerland |
Creel Type | v-type | v-type | v-type | |
4 | Creel Capacity | 1224 | 720 | 1080 |
5 | No of Rods | 136 | 144 | 120 |
6 | No of Pegs per Rod | 09 | 05 | 09 |
components of Creel :
- Spindle
- Tension Rod
- Stop Motion Assembly
- Guide Rod
- Cone/Cheese
- Yarn clearer
- Indicator
Spindle :
- The required packages, which weigh between 2.5 and 6.25 pounds each, are hung on it
Tension Rods :
- These rods are mounted on a rail and move back and forth to prevent yarn slackness during speed changes or when the machine stops.
- The tension of the yarn adjusts based on the movement of these rods.
Stop Motion Assembly :
- It is an electronic sensor designed to stop the machine if the warp yarn breaks. It consists of a transmitter and receiver through which the yarn passes. The sensor also functions as a pre-tensioner when the machine restarts after a stop. Pneumatic pressure is used to open and close the clutch, applying pre-tension to the yarn. Every 2-3 seconds, air is blown into the stop-motion assembly to clear any fluff. When the machine restarts, the clutch remains open for 10 seconds.
Indicators:
- There are two rods with indicator bulbs on top of the creel. If the bulb on the right-side rod lights up, it means the yarn on the right side is broken. Each spindle has a set of 9 numbered bulbs (1-9). The number on the bulb corresponds to the cone of that particular rod.
Plate In Front of Creel:
- The monitor on the front of the creel displays four types of information. The first digit indicates the wing number, the second digit shows the cone number, and the third and fourth digits represent the rod number.
Head Stock:
Expandable Comb:
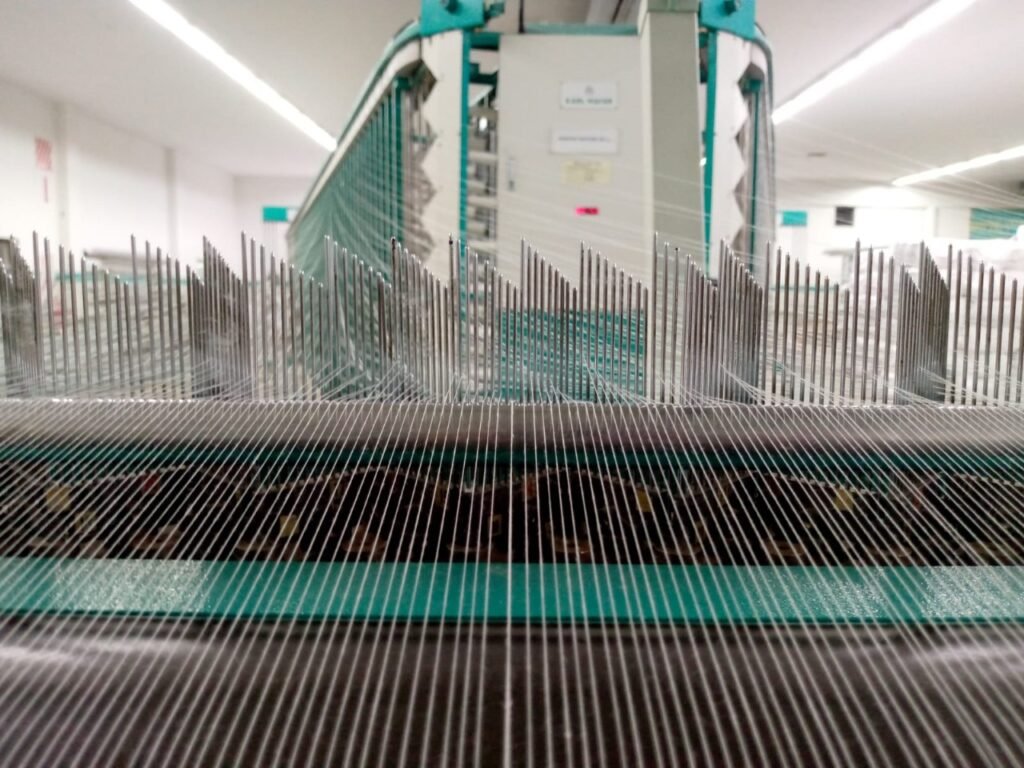
- Expandable comb
- Guide Roller
- Pressure Roller
- Beam Bracket
- Automatic Knock-Off
- It evenly distributes the yarn across the width of the warp and guides it along a fixed path.
Guide Roller:
- It directs the yarn towards the beam.
- The operator can also monitor any thread breakage from its surface.
Pressure Roller:
- Apply the necessary pressure to the warp yarn to create friction and drive the beam.
Beam Bracket:
- It holds the beam in place during the process.
Automatic Knock-Off:
It activates and stops the machine automatically once the required length is achieved.
Pneumatic Pressure at Machine::
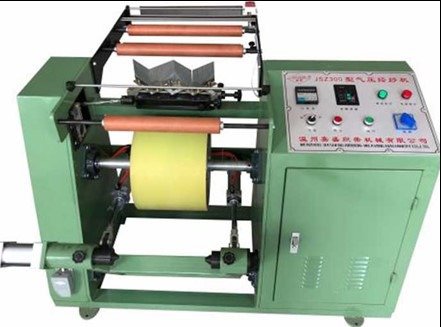
The pneumatic pressure system is applied in the following operations:
- Engaging and disengaging the clutches of the WSM.
- Operating the fluff removal system at the WSM.
- Actuating the drum press.
- For rod blowing applications.
- Facilitating the movement of tension rods.
Warping Calculations::
During the warping process, a bag of yarn cones is received, and the weight of each cone is measured initially for further calculations.
Weight of cone.:
To determine the weight of each cone, the weight of the bag is initially measured.
If The 100-Pound bag contains 24 cones.
No of bag = 01
Weight of bag = 100 pounds
No of Cones in it = 24
Weight of each cone = weight of bag / No of cones
Weight of each cone = 100 / 24
Weight of each cone = 4.167 pounds.
Length of cone:
The length of a yarn cone can be calculated by knowing the yarn count and the total weight of the cone
What method can we use to measure the yarn count of a cone?
To accurately measure the yarn count, it is recommended to send the cone to a specialized laboratory. Upon receiving the detailed test report, we can continue our operations with precise knowledge of the yarn count and on the other hand it is written on the received yarn bags as well.
Length of cone = (Yarn count) (768.1)(weight of cone)
From where we get 768.1 values in this formula?
To calculate the cone length in meters, we first convert yards to meters using a conversion factor of 0.9144 meters per yard. For a cone of 840 yards:
- Length in meters = 840 yards × 0.9144 meters/yard = 768.096 meters
Next, we calculate the total length of the cone based on the specified dimensions and conversion factors. Assuming a cone with a 16:1 ratio of length to diameter, and a diameter of 4.167 meters, the total cone length is:
- Total cone length = (16 / 1) × 768.096 meters × 4.167 meters = 51,210 meters
However, considering that we can only utilize 99% of the cone’s length, the usable length becomes:
- Usable cone length = 51,210 meters × 0.99 = 50,697 meters
No of beams Calculation Formula:
The number of beams is calculated using a simple division formula. By dividing the total number of ends by the capacity of a single creel, we can determine the exact number of beams required. In this specific scenario, with 18,700 ends and a creel capacity of 1,224, we need 15 beams to accommodate all the ends.”
No. of beams = Total ends / Creel capacity
No. of beams = 18700 / 1224
No. of beams = 15 beams
Total ends Required for Each beam:
The number of total ends / beams is calculated as:
No. of ends / beam = Total Ends / No. of beams
No. of ends / beam = 18700 / 15
No. of ends / beam = 1247 ends:
No of yarn bags Required to complete 8500 Order pcs:
No. of bags = order × Total ends / 768.1 × count × 99
No of bags = 8500 × 18700 / 768.1 × 40 × 99
No of bags = 52 bags.
the process of warping:
- Start by obtaining a bag of cones.
- The yarn count is specified on the bag.
- Calculate the weight of each cone based on the total bag weight.
- Use this weight measurement to determine the length of yarn on each cone.
- Place the cone onto the creel of the warping machine.
- Set the warping machine according to the required specifications.
- Attach the yarn from each cone to the warping machine.
- Begin the warping process to wind the yarn onto the beam.
- Adjust the tension during the process based on the yarn count.
- The correct tension will cause weaker yarn to break.
- For a 40/1 yarn count, set the tension to 14 on the Karl Mayer machine.
- Aim to use 99% of the yarn length from each cone.
Reasons of Yarn breakages on warping machine:
- Due to Weak Yarn
- Slub In yarn
- Spice open
- Cut on yarn Cone
- Ribboning
- Double End
- Sloughing off
- Contamination
- Defective Cone package.
Conclusion:
The warping process begins by attaching a bag of cones to the creel of a warping machine. The desired number of ends is programmed into the headstock, which controls the winding process. The machine then winds the yarn onto a beam until it is full. Once a beam is completed, it is ready to be transferred to the sizing machine for further processing. The total number of beams that can be warped is limited by the capacity of the sizing machine.
продвижение сайтов https://www.prodvizhenie-sajtov15.ru/ .
Ивенты в торговых центрах подарят вам позитивные впечатления. Образовательные семинары обогащают открыть новые горизонты. Театральные постановки с полным погружением вдохновляют. Подбирайте для незабываемых ивентов с семьей!
Заказать билеты на театральное представление