Weaving loom:
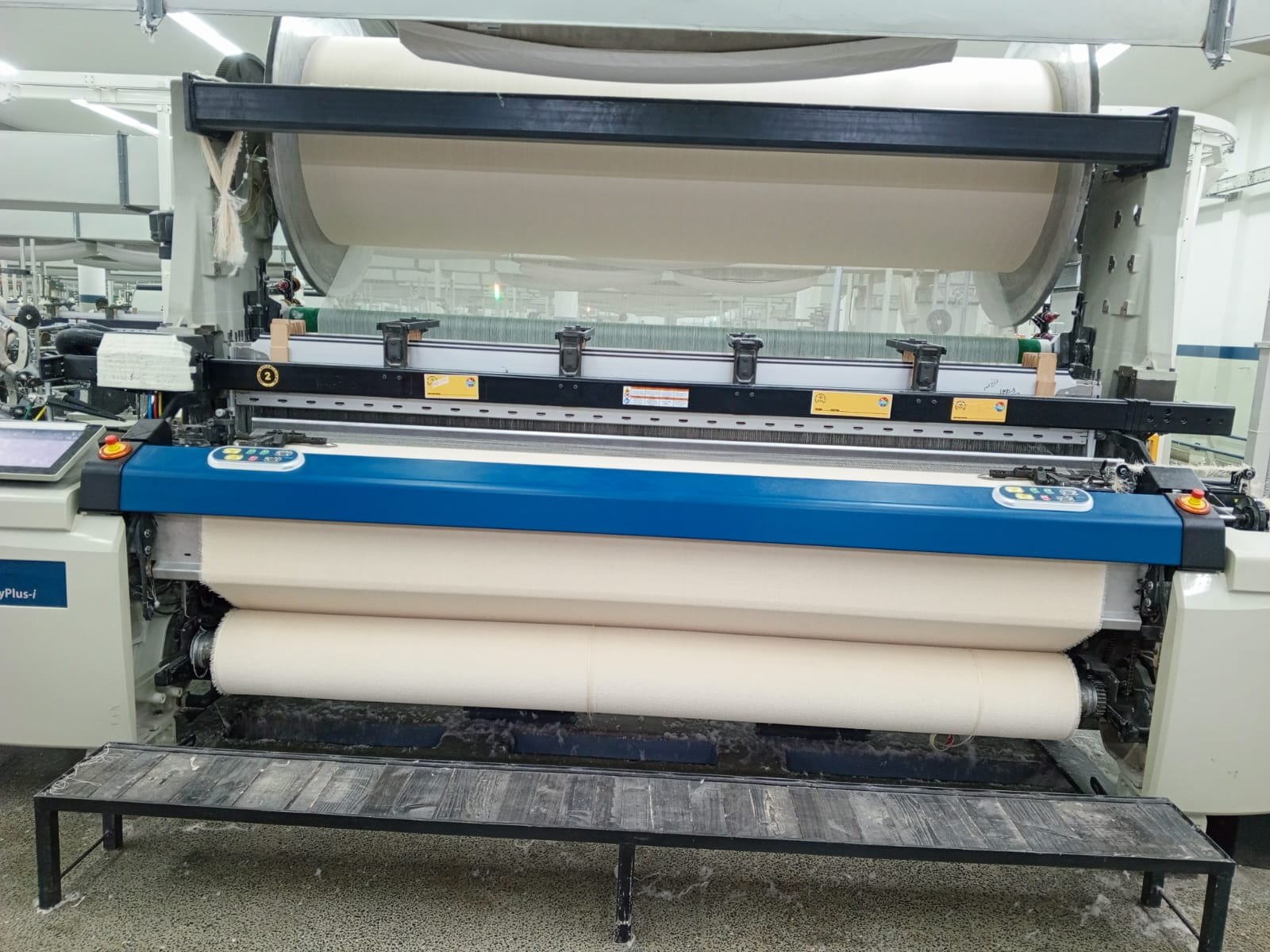
The machine responsible for creating fabric is known as a weaving loom. This device weaves fabric by intertwining warp and weft yarns. The warp yarns are threaded through the warp beam, while the weft yarn is supplied through various methods such as projectiles, air jets, or water jets weft through mechanisms.
History of Weaving Loom:
The evolution of weaving loom has a long history, beginning with primitive or vertical looms, followed by pit looms and frame looms. These early looms utilized shuttles and fly shuttles. Progressing further, Chittaranjan and Hattersley loom marked a significant step as semi-automated looms. Subsequently, ordinary power looms and automatic power looms with automated mechanisms were introduced. The latest advancements include modern looms equipped with projectile, air jet, and water jet technologies, introducing innovative weft-throwing mechanisms.
History of Weaving on Weaving Loom:
The history of woven fabrics dates back around 6000 years, with the Egyptians creating them during that time. Chinese craftsmanship advanced significantly over 4000 years ago when they produced fine fabrics from silk.
In the 3rd century, China introduced the shedding mechanism, a crucial innovation that eventually made its way to Europe. By the 12th century, fully wooden hand looms became standard designs in England, marking a significant milestone in the evolution of weaving technology.
Over the past 850 years, continuous developments have occurred in the design and performance of looms. In 1733, John Kay’s invention of the hand-operated fly shuttle played a pivotal role in boosting productivity. This shuttle, equipped with four wheels, moved along the lower side of the warp sheet. Operated by the weaver using two wooden tenders connected to a small cord, it was a major leap forward in efficiency.
In 1785, E. Cartwright introduced the power loom, ushering in a new era of mechanized weaving. As technology progressed, steam power became integral to cast iron looms in the early 1800s. By the 1830s, England boasted around 100,000 shuttle looms in operation.
In 1895, the invention of electrically driven looms marked a significant advancement. By the beginning of the 1930s, a revolutionary concept emerged, where each weaving machine was individually powered by an electric motor. This concept has endured and remains in use today, showcasing the continuous innovation in the field of weaving technology.
List of Modern weaning loom:
SR # | Name of Weaving Loom | Comany | Origion |
---|---|---|---|
01 | Picanol Group | Belgium | |
02 | Toyota Industries Corporation | Japan | |
03 | Sulzer | Switzerland | |
04 | Itema | Italy | |
05 | Tsudakoma Corporation | Japan | |
06 | Somet | Italy | |
07 | Lindauer DORNIER GmbH | Germany | |
08 | Stäubli International AG | Switzerland |
Basic Mechanism of weaving on the Weaving Loom:
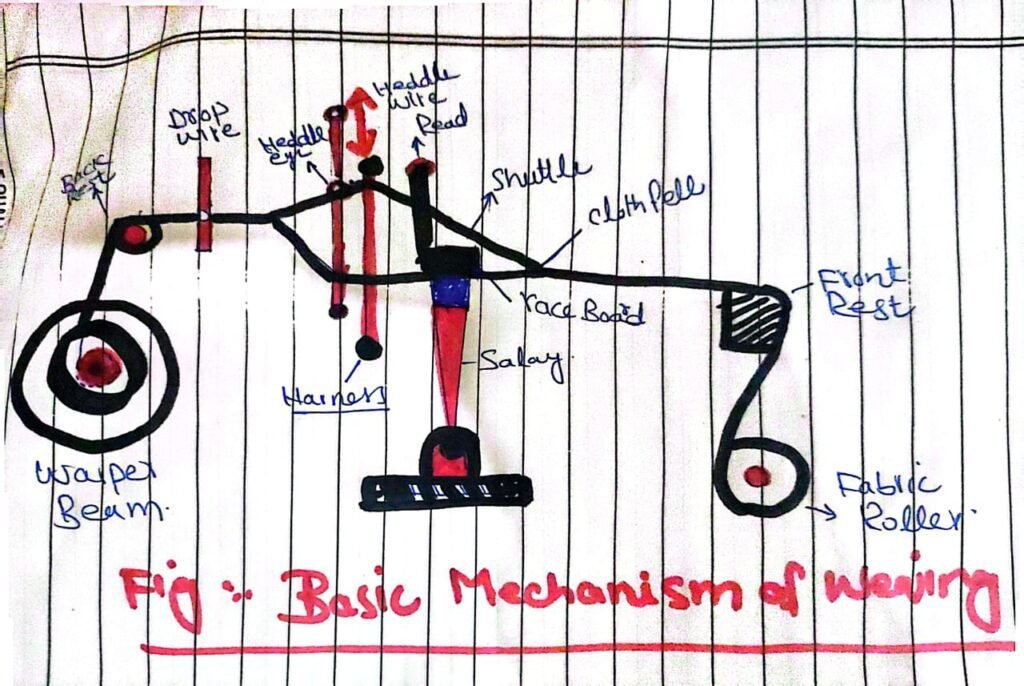
- The wrapper threads unwind from the wrapper beam, pass through the backrest, and then extend to the held frames, also known as the Harness Frame. These frames serve the purpose of separating the warp yarns into sheets, facilitating the formation of the shed.
- The wrapper threads continue their journey through the reed on the loom. The reed serves two important purposes: it maintains a consistent spacing of the threads and aids in compacting them when the final pick is inserted.
- Following the beat-up process, all the threads come together again in the fabric at a specific point known as the “point of the cloth fell.”
- After the weaving process, the woven cloth or fabric moves over the front rest and is wound onto the cloth roller or fabric roller.
- In case the warp yarn breaks during beat-up, shedding, or the weaving process, a dropper wire signals an immediate stop to the loom. The weaver, overseeing the entire process, then knots the broken end on the loom before resuming its operation.
Fabric Manufacturing Process on Weaving Loom:
Warp Yarn preparation:
Warping is a procedure to organize yarns lengthwise on the loom. In the warping process, the warp yarns are systematically wound parallelly onto a beam, known as the warper beam. This warper beam becomes the input material for the sizing process.
Sizing Process in weaving:
The sizing process follows the warping process, where the warper beam becomes the input for sizing. After sizing, the sizer beam is prepared for use in the weaving process. During sizing, a proactive adhesive, which can be natural or synthetic, is applied to the yarns. This adhesive application serves the purpose of reinforcing the yarns, allowing them to endure the abrasion and tension experienced on weaving looms during shedding, beat-up, and weaving. By strengthening the yarns, the likelihood of yarn breakages is minimized, enabling the weaving process to achieve maximum RPM and speed on the weaving looms. This, in turn, enhances efficiency and production.
Drawing in process in weaving:
The weaving drawing-in process involves two steps: drafting and denting. In drafting, the ends pass through the eye of the heald wire or harness as per the draft plan. Two individuals, the Reacher, and the drawer, work together to accomplish this task. During denting, the warp ends pass through the dents of the reed in alignment with the denting for the fabric to be woven. This step can be completed by one or two persons. While the drawing-in process can be done manually, in organized facilities, machines are employed to ensure maximum production and accuracy.
Looming process in weaving on the weaving loom:
The procedure of getting the loom ready before beginning the weaving is known as looming. It encompasses the drawing-in process, gaiting, and knotting. As the Drawing process is defined above we will only cover the gaiting and knotting process below.
Gaiting in the weaving process on the weaving loom:
After finishing the drawing-in, drafting, and denting processes, the loading of heald frames, reeds, drop wires, and weaver’s beam onto the weaving looms for the upcoming steps is known as the gaiting process in weaving.
Tying Inn / Knotting in the weaving process on the weaving Loom:
The process of connecting the warp threads from the old warp beam to introduce a new warp is known as tying and knotting. This task can be carried out manually or with the assistance of knotting machines. It is crucial to perform this process accurately to ensure there is no variation in the count of the warp yarn, and that the number of yarns on the new beam matches the number on the old beam.
Frequently asked questions on weaving loom:
What is the basic function of a weaving loom?
A weaving loom is a machine designed to interlace threads, creating woven fabric. It facilitates the process of turning yarn into cloth by interlacing the warp (longitudinal) and weft (transverse) threads.
What are the key components of a weaving loom?
The main components include the warp beam, heddles, healds, shuttle, reed, and the fabric or cloth beam. These elements work together to enable the systematic interlacing of threads during the weaving process.
How has weaving technology evolved over the years?
Weaving technology has evolved significantly, from early manual looms to sophisticated automated machines. Innovations include the introduction of shedding mechanisms, power looms, and, more recently, computerized looms that enhance efficiency and precision .for towel manufacturing two beams are used on loom for ots weaving.one for ground yarn and the other one for the pile yarns.
What role does a shuttle play in traditional weaving loom?
In traditional weaving looms, the shuttle is a crucial component that carries the weft yarn through the shed created by the raised and lowered warp threads. This process is essential for forming the fabric’s structure.
How do modern advancements, such as computerized looms, impact weaving efficiency?
Computerized looms integrate advanced technology to automate and control the weaving process. These machines offer increased speed, precision, and the ability to execute complex patterns. The result is enhanced efficiency and production capabilities in textile manufacturing.
You gathered all that information in this article that I was learning. Good job!
thank you very much for your appreciation.
Преимущества профессиональной мойки двигателя в Москве, подскажем, как сделать выбор.
Мойка двигателя от масла и грязи dvigatel-moyka.ru .
Идеальная комплексная мойка авто: секреты профессионалов, экспертное мнение.
Комплексная мойка автомобиля цены Москва moyka-kompleks.ru .
Как избавиться от вмятин на кузове без покраски, Избавляемся от вмятин на кузове: просто и быстро
Исправление вмятин на автомобиле без покраски https://www.remont-vmyatin-bezpokras.ru .
Лучшая комплексная мойка в вашем городе, чтобы ваши ожидания были полностью удовлетворены.
Комплексная мойка авто https://www.kompleks-moyka.ru/ .
Качественная мойка двигателя в столице, почем стоит?
Детейлинг двигателя автомобиля в Москве https://www.moyka-motor.ru/ .
Экономим на ремонте: убираем вмятины на кузове автомобиля самостоятельно, самостоятельно и качественно.
Убрать вмятины на кузове автомобиля без покраски http://vmyatina-remont.ru/ .
Освежите свою мебель дома в Москве, надежно и качественно.
Химчистка обивки http://www.mebel-clean-order.ru/ .
Преимущества чистки мебели в домашних условиях, о которых вам следует знать.
Химчистка клининг https://www.price-mebel-clean.ru .
Эффективное очищение мебельных элементов без усилий, для вашего удобства и комфорта.
Чистка мебели cleaning-mebel-order.ru .
Подарите вашей мебели новую жизнь с химчисткой на дому в Москве.
Химчистка ковров мебели дивана https://www.dom-clean-price.ru/ .
great work —-keep it up
https://reminiapk.app/
Как избежать негативных последствий от процедуры химчистки мебели на дому, советы от экспертов.
Клининг химчистка мебели http://mebel-cleaning-co.ru/ .
Как выездная химчистка мебели преобразит ваш интерьер, делая его привлекательным и ухоженным.
Профессиональная химчистка мягкой мебели на дому Москва http://vyiezd-himchistka.ru/ .
Освежите свою обивку без лишних хлопот, без усилий и стресса.
Химчистка мебели покрытий https://himchistka-site.ru/ .
Качественная выездная химчистка мягкой мебели по выгодной цене со скидкой для постоянных клиентов.
Химчистка на дому недорого Химчистка на дому недорого .
Как провести безопасную химчистку мебели в домашних условиях, которые стоит знать.
Как выбрать безопасные средства для химчистки мебели, которые безопасны для здоровья.
Экспертный подход к безопасной химчистке мебели, который гарантирует качественный результат.
Какие опасности могут поджидать вас при химчистке мебели, как оградить себя от неприятностей.
Инновационные методы безопасной химчистки натуральной мебели, с рекомендациями экспертов.
Безопасная химчистка мебели – https://safe-clean-mebel.ru/ .
Оптимальное решение для чистки матрасов дома, для поддержания безупречной чистоты в вашей спальне.
Химчистка матрасов с выездом на дом himchistka-matras-dom.ru .
Как избавиться от пятен на матрасе и пролитье жидкости.
Дезинфекция матраса – http://www.dezinfekciya-matras-msk.ru .
Как вернуть матрасу чистоту и свежесть?
Матрас икеа химчистка – https://www.matras-ikea-himchistka.ru .
Химчистка для матрасов высокого класса
Химчистка премиум матрасов – http://www.himchistka-premium-matras.ru/ .
Как выбрать материал для ремонта кожаной мебели?
Восстановление кожаного дивана http://restavracya-kozhany-mebel.ru/ .
Сохраняем кожаную обивку без больших затрат, полезные советы
Восстановление кожаной мебели https://divan-kozha-remont.ru/ .
Эффективные методы очистки кожаной мебели от пятен на дому, чтобы не повредить материал.
Чистка кожаной мебели на дому – https://himchistka-kozhany-mebel.ru .
Топ-5 ошибок при химчистке антикварной мебели.
Химчистка антикварной мебели – http://himchistka-antique.ru .
радиаторы отопления трубчатые вертикальные купить http://www.vertikalnyeradiatory.ru/.
10 шагов к безупречной чистоте мягкой мебели в офисе, которые помогут убрать пятна и пыль.
Химчистка мягкой мебели в офисе – mebel-office-clean.ru .
Специалисты доступны круглосуточно.
Чистка ковров и диванов на дому https://himchistka-divan-kover.ru .
Надежная химчистка ковров и мягкой мебели на дому, доверьтесь профессионалам.
Химчистка ковров и мебель цены Химчистка ковров и мебель цены .
Сравните цены на экспертизу зданий и сооружений, выберите выгодное предложение.
Строительно техническая экспертиза квартиры для суда стоимость https://konstruktexpert.ru/ .
Как стать успешным инженером: секреты профессионалов, которые помогут вам достичь высоких результатов.
Технический инжиниринг – proektzdanie.ru .
Какие недочеты чаще всего выявляют при проверке сметы на соответствие?, Основные критерии соответствия сметы.
Проверка смет на строительные работы – http://www.smeta-control.ru/ .
Почему стоит выбрать профессиональную экспертизу фасада здания .
Обследование фасада административного здания – https://fasadexpertiza.ru/ .
Выводы из практики контроля качества стройматериалов на производстве.
Входной контроль материалов на строительной площадке – https://vkhodnoykontrol.ru/ .
Как обеспечить надежность несущей стены, что нужно знать о проведении экспертизы.
Экспертиза стен здания – https://stenexpert.ru .
Индивидуальный подход к каждому клиенту, опытные специалисты.
Эксперт строй инжиниринг – http://www.kvalstroi.ru/ .
Секреты успешного проведения строительной экспертизы.
Бюро строительных экспертиз – Бюро строительных экспертиз – .
Надежная защита Вашего строения с помощью строительной экспертизы.
Эксперт строительной экспертизы – https://diagnostikastroi.ru .
Важность компании по проведению строительной экспертизы, как избежать ошибок?.
Компания строительная экспертиза – https://www.prozdaniemon.ru/ .
Тайны успешного обследования строительных конструкций здания, которые вы должны знать.
Обследование состояния строительных конструкций здания – https://www.konstruktest.ru/ .
Прибыльные аспекты строительной экспертизы, строительная экспертиза: важный этап строительства.
Эксперт строительной экспертизы – https://www.rabotest.ru .
Советы по выбору тестов для бетона, для достижения лучших результатов.
Лаборатория испытания бетона https://betontestlab.ru .